
ZW3D - CAD / CAE / CAM
Design, construction, simulation and production on one platform.
3D CAD/CAE/CAM | Zum unschlagbaren Einmalpreis ab 1875€ | Hochflexibel erweiterbar | Optimal mit GAIN Collaboration PDM
ZW3D
Leistungsstarkes und schnelles CAD:
Mehr als eine Alternative zu AutoCAD®.
ZW3D is an easy-to-learn all-in-one 3D CAD/CAE/CAM solution that offers a wide range of functions for product development, mechanical engineering and plant planning. ZW3D offers everything you need to turn your ideas into reality. From design to simulation to manufacturing and far beyond - with a sustainable increase in productivity.
Erstklassige Funktionalität zum fairen Preis.
ZW3D ist zu einem unschlagbare Einmalpreis erhältlich – keine jährlichen Lizenzgebühren.
Kontaktieren Sie uns für eine unverbindliche Demo – wir zeigen Ihnen, wie einfach Effizienz sein kann. Ihr GAIN Team.
- Professionelles CAM-CAE-System
- Hervorragende Alternative zu INVENTOR®
- Attraktiver Einmalpreis anstatt Miet-Lizenz
- Bekannte Bedienung und Oberflächen
- DWG- und DXF-kompatibel
- Deutlich verbesserte Performance

ZWSOFT: 2D / 3D Design + Konstruktion
CAD-Lösungen, die mehr leisten und weniger kosten.
ZWSOFT ist ein weltweit etablierter Anbieter von CAD-/CAM-Lösungen mit über 20 Jahren Erfahrung in der Entwicklung leistungsstarker und kosteneffizienter Software für Konstruktion und Fertigung. Die Hauptprodukte, ZWCAD und ZW3D, zeichnen sich durch hohe Kompatibilität, Benutzerfreundlichkeit und Stabilität aus und bieten eine attraktive Alternative zu etablierten CAD-Systemen. Als Vertriebspartner bieten wir Ihnen Zugriff auf innovative Technologien, flexible Lizenzmodelle und zuverlässigen Support – ideal für Unternehmen, die auf Qualität und Effizienz setzen.
More productivity, less costs
Thanks to extensive design and simulation tools, users and companies can shorten the development time of new products, systems and machines, save costs and accelerate innovation. ZW3D offers powerful functions such as hybrid volume-surface modeling, structural simulation, 2 to 5 axis machining and special tools for machining and setting sheet metal workpieces, molds and much more. ZW3D offers everything you need to turn your ideas into reality.
Typical application areas
Optimized plant planning
from 2D drawing to structural analysis through industry-specific modules for metal and sheet metal processing, steel construction, cable organization and much more.
Efficiently design injection molds on one platform. Comprehensive tools for mold analysis, standard mold parts, specialized design features and mold fundamentals.
Optimized import and export functions from industry standards such as CATIA and NX and many other systems.
Direct import from Rhino, Creo and other popular design solutions. Simulation-based validation of the structural strength of the design.
Creation of machining strategies for manufacturing parts and tools with 2-, 3- and 5-axis milling. Free adaptation of the postprocessor to different machine tools.
ZW3D 2026 ist da - noch besser, noch schneller, noch vielseitiger.
Buchen Sie jetzt Ihre unverbindliche Vorführung.
Highlights CAD
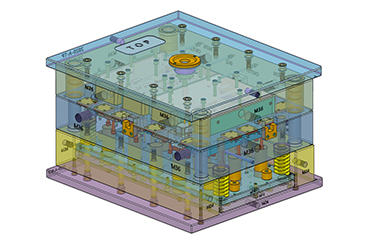
ZW3D covers the entire process of plastic mold design with data repair, product manufacturability analysis, quick parting, standard mold base libraries, automatic drawing, electrode design and more.
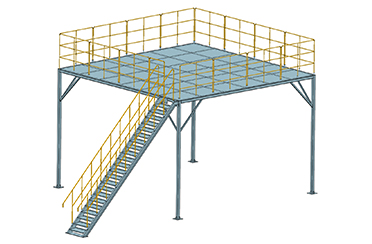
ZW3D provides various standard and non-standard profile types. ZW3D can quickly change the connection types of the structure, add profile elements and create a structure cutting list.
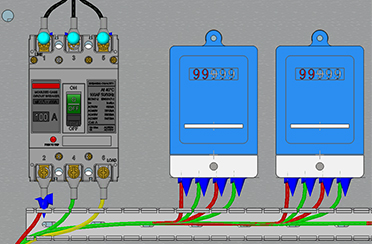
ZW3D can plan, modify and manage wire harnesses, allowing you to complete wire harness design in a shorter time.
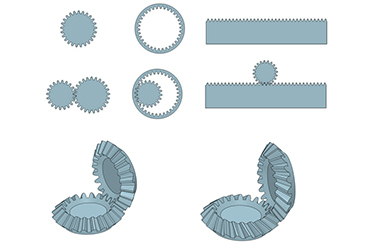
ZW3D can create spur gears, bevel gears, worms and wheels as parts or assemblies and adjust the parameters at all levels.
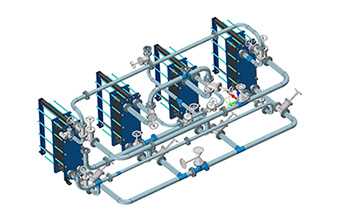
With a variety of piping routing methods, a library of standard parts and the automatic addition of flanges, gaskets and connections, ZW3D covers all aspects of piping planning.

Turn objects into sketch blocks and create new objects by inserting and resizing blocks.
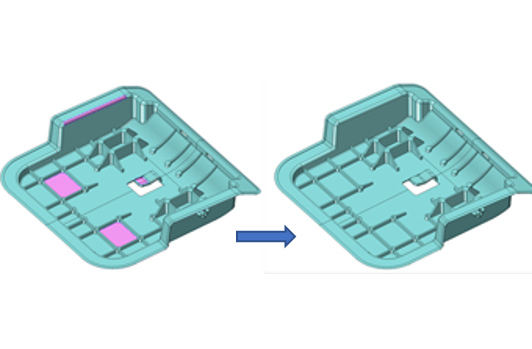
Analyze and repair incorrect conditions (e.g. open edges, gaps, duplicate faces, intersection loops) that exist in the geometry of imported files.
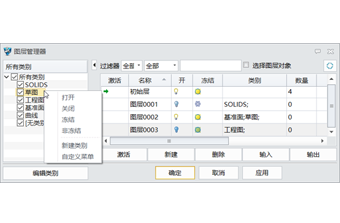
Schnelles Sortieren und Organisieren von Modell-Features in 3D: Einfaches Anordnen von Layern über das Attribut Kategorie, Steuern und Bearbeiten von Layern mit den Funktionen Filter und Select Object in Layer.
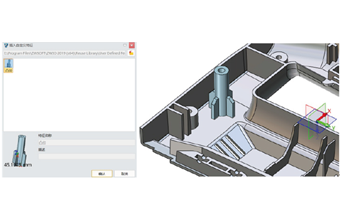
Create a feature with all the properties of geometries so that you can easily reuse them and avoid redundant work steps.
Highlights CAM
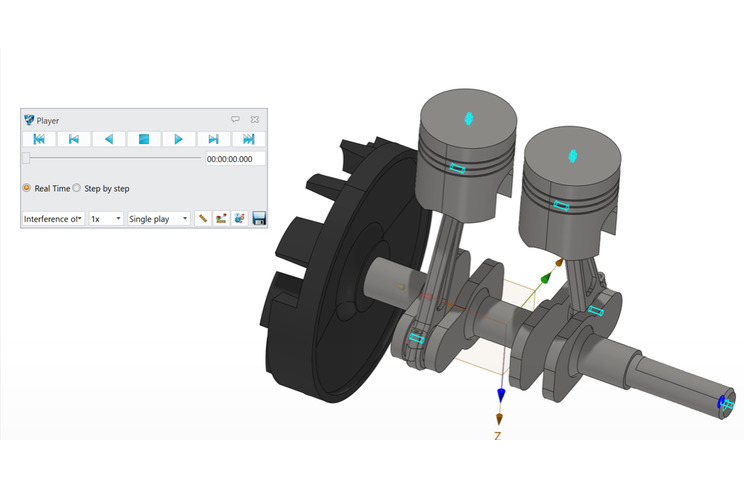
Efficiently creating motion mechanisms facilitates dynamic interference testing, trajectory simulation, and motion data table generation.
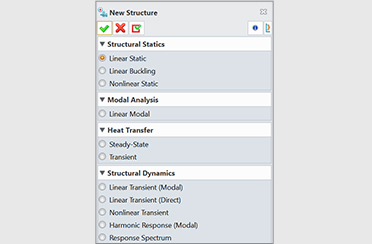
ZW3D supports linear static analysis, bending analysis, modal analysis, dynamic analysis, nonlinear analysis, fatigue analysis and heat transfer analysis to meet different requirements.
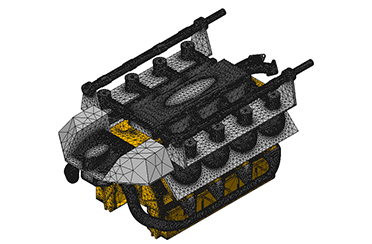
ZW3D provides a variety of divisible geometric unit types, including curves, triangles and tetrahedrons, to meet the different needs of structural meshing.
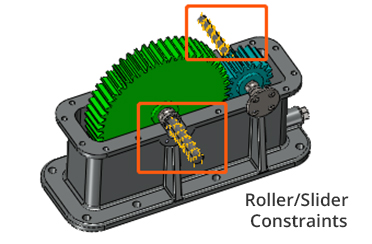
ZW3D supports constraints such as fixed restraints, rollers/sliders and fixed hinges, structural loads such as force, pressure, torque, line load and gravity, and thermal loads such as temperature, heat power, heat flux, convection and thermal radiation.
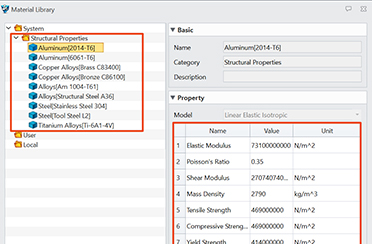
You can easily access commonly used materials and customize material properties to suit your specific needs.
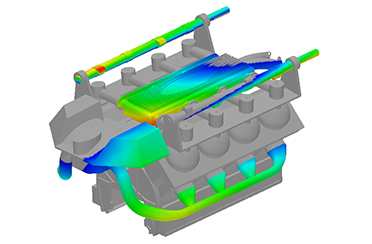
The simulation results can be presented in various ways, such as result clouds, lists, and animations. You can also customize the results, review results, and create reports on simulation results.
Highlights CAE
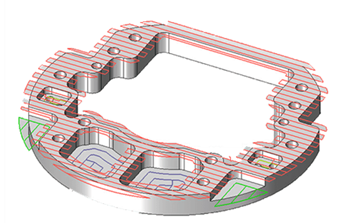
Features such as holes, grooves and steps in parts can be automatically detected so that efficient drilling programs and milling paths can be created according to the user's requirements, significantly reducing programming time.
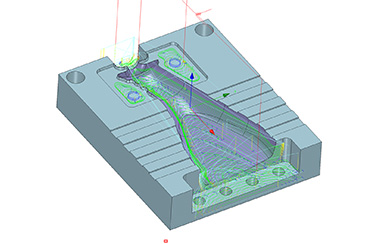
Volumill™ for ZW3D can help create optimized toolpaths that save 50-80% of cycle time. It also allows full milling depth to be utilized, reducing cutting tool costs by up to 75%.
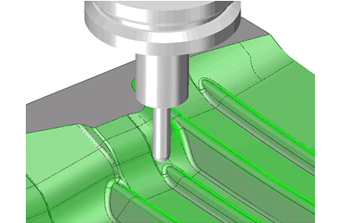
Over 40 types of 3X-controlled machining processes are available, allowing you to easily handle all types of manufacturing tasks. With QuickMilling, it is easy to create smooth toolpaths that guarantee high-quality surfaces.
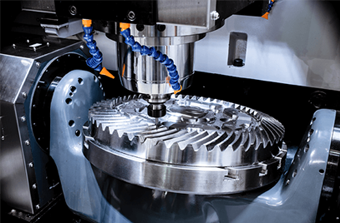
A complete indexing and 4-5 axis machining solution is available that can work with STL files. You can efficiently use features such as chips, drive curve, flow cut, etc. to produce precise parts.
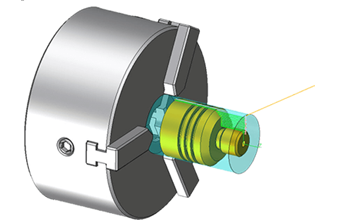
Internal and external roughing, finishing, grooving, threading, facing and drilling are easy to use and useful for machining most turned parts. Turning cycles, simulation and verification accelerate the transition from manual programming to safe machining.
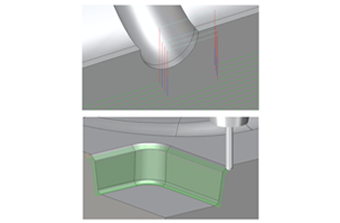
Achieve better toolpaths, improve machining efficiency, and avoid tedious parameter adjustments and toolpath recalculations. The entire or partial toolpaths can be flexibly edited with tools such as trimming, reordering, relinking, extending, and transforming.
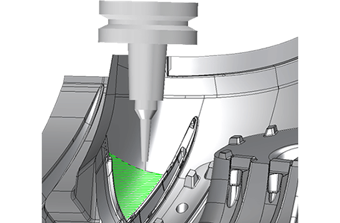
Wireframe simulation, Solid Verify and full machine simulation enable reliable, efficient and safe machining by detecting collisions, analyzing backlogs, etc. to avoid machine damage, poor quality and late deliveries.
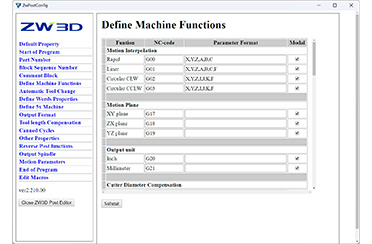
ZW3D comes with more than 80 standard postprocessors compatible with all kinds of CNC milling and lathe machines. Professional and localized postprocessor support is always available.
Variants
Feature | Fundamental | Standard | Professional | Advanced | 2-Achsen Machinist | 3-Achsen Machinist | Premium |
---|---|---|---|---|---|---|---|
CAD-Funktionen | |||||||
Converter for IGES, Parasolid®, STEP, DWG/DXF, VDA, STL files, etc. | ✔ | ✔ | ✔ | ✔ | ✔ | ✔ | ✔ |
Open, save and edit directly: CATIA®, Inventor®, NX®, SolidWorks®, SolidEdge®, Creo®/ProE® and ACIS files | ✔ | ✔ | ✔ | ✔ | ✔ | ✔ | ✔ |
3D printing interface | ✔ | ✔ | ✔ | ✔ | ✔ | ✔ | ✔ |
2D, 3D sketches and curves | ✔ | ✔ | ✔ | ✔ | ✔ | ✔ | ✔ |
Parametric hybrid modeling of volumes and surfaces | ✔ | ✔ | ✔ | ✔ | ✔ | ✔ | ✔ |
Volume modeling | ✔ | ✔ | ✔ | ✔ | ✔ | ✔ | ✔ |
Assemblies | ✔ | ✔ | ✔ | ✔ | ✔ | ✔ | ✔ |
Data analysis and geometry healing | ✔ | ✔ | ✔ | ✔ | ✔ | ✔ | ✔ |
Direct editing | ✔ | ✔ | ✔ | ✔ | ✔ | ✔ | ✔ |
2D Drawings | ✔ | ✔ | ✔ | ✔ | ✔ | ✔ | ✔ |
PMI 3D dimensioning | ✔ | ✔ | ✔ | ✔ | ✔ | ✔ | ✔ |
Library for standard parts | ✔ | ✔ | ✔ | ✔ | ✔ | ✔ | ✔ |
TraceParts online parts library | ✔ | ✔ | ✔ | ✔ | ✔ | ✔ | ✔ |
Specialized module | |||||||
Sheet metal processing | ✔ | ✔ | ✔ | ✔ | |||
Steel construction and welding | ✔ | ✔ | ✔ | ✔ | |||
Point cloud | ✔ | ✔ | ✔ | ✔ | |||
Structure construction | ✔ | ✔ | ✔ | ✔ | |||
ZW3D movement | ✔ | ||||||
Wiring harness construction | ✔ | ||||||
ECAD/MCAD collaboration | ✔ | ||||||
Piping construction | ✔ | ||||||
Electrode construction | ✔ | ✔ | |||||
Mold making | ✔ | ✔ | |||||
CAM | |||||||
Drilling | ✔ | ✔ | ✔ | ||||
Automatic processing | ✔ | ✔ | ✔ | ||||
2-axis turning | ✔ | ✔ | ✔ | ||||
2-axis milling | ✔ | ✔ | ✔ | ||||
Tool path editor | ✔ | ✔ | ✔ | ||||
Volume simulation | ✔ | ✔ | ✔ | ||||
ZW3D Postprocessor | ✔ | ✔ | ✔ | ||||
NC program (G-code) output | ✔ | ✔ | ✔ | ||||
3-axis QuickMill™ | ✔ | ✔ | |||||
SmoothFlow™ adaptive feed control | ✔ | ✔ | |||||
Verfügbare Zusatzmodule (zusätzlicher Kauf erforderlich) | |||||||
JT format input / output | ✔ | ✔ | ✔ | ✔ | ✔ | ✔ | |
CATIA®, SolidWorks®, Creo® 2D drawings les | ✔ | ✔ | ✔ | ✔ | ✔ | ✔ | |
PARTsolutions library for standard parts | ✔ | ✔ | ✔ | ✔ | ✔ | ✔ | |
KeyShot® Rendering | ✔ | ✔ | ✔ | ✔ | ✔ | ✔ | |
FEA Fenite Elemente Analyse | ✔ | ✔ | ✔ | ✔ | ✔ | ✔ | ✔ |
VoluMill™ HSC roughing | ✔ | ✔ | ✔ | ||||
4- & 5-axis milling | ✔ | ✔ | |||||
Complete machine simulation | ✔ | ✔ | ✔ |
Would you like to find out more, do you have any questions or suggestions?
Über dieses Formular können Sie eine unverbindliche Produktpräsentation buchen und Downloads zu unverbindlichen Demo-Versionen erhalten. Unsere Produktspezialisten werden sich zeitnah bei Ihnen für eine Terminabstimmung melden. Wir bedanken uns für Ihr Interesse.
Ihr GAIN-Team.
GAIN-Newsletter
Wir informieren Sie über neue Produkte sowie zu Trends konstruktionsintensiver Branchen.
Die Registrierung für unseren Newsletter erfordert durch die DSGVO eine gesonderte Bestätigung per E-Mail. Sie können diese jederzeit widerrufen.