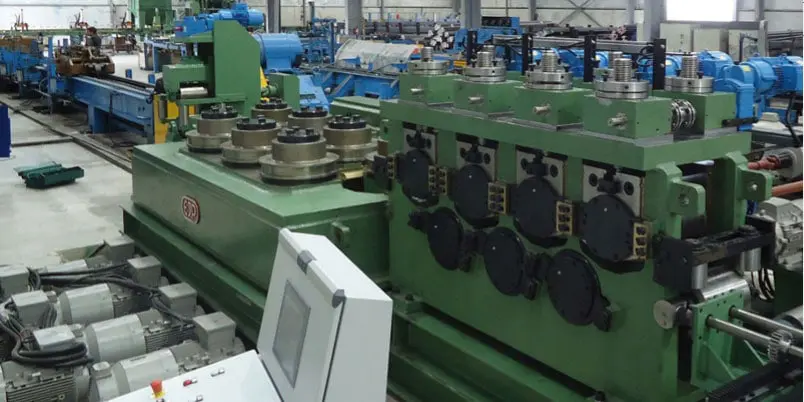
PDM replacement from Productstream Professional to GAIN Collaboration
In October 2017, support for the product data management solution Autodesk Productstream Professional (PSP) was officially discontinued.
Many affected companies were looking for a PSP successor - an equivalent solution. This was also the case for EJP Maschinen GmbH, headquartered in Baesweiler in the Rhineland.
With a short, intensive support from consultation to PDM introduction, the GAIN Software system partner cubikom helped EJP Maschinen GmbH to make a comprehensive, updated switch in terms of drawing creation and management. With a happy ending, because the task was a challenge.
36,000 linked drawing data under PSP
Designers at EJP Maschinen GmbH work with Autocad Mechanical and Autodesk Inventor. Over the years, around 36,000 drawing files have been created.
The drawing data was initially managed using the product data management solutions "Compass" and its successor product Autodesk Productstream Professional. This drawing data is also linked to machine- and customer-specific data and information such as contracts, customer correspondence or parts lists from Excel. All of this data belongs to customer orders.
The challenge: Adoption of very specific data architectures
A special requirement for cubikom was the 1:1 transfer of the grown structures created by Compass with the company-specific links.
Links that map the internal structure, the machines, commission numbers and customer names. At EJP Maschinen GmbH, we are used to being able to search not only by numbers, but also by customers or machines sold to customers. If a machine has been sold multiple times, it is also linked to multiple customers.
Open heart surgery
Dipl.-Ing. Robert Jungbluth, Head of the Development Department at EJP Maschinen GmbH:
"Our task was quite special: All data, especially its multi-layered connections, had to be transferred to a new system. Just imagine if the connections had changed in the process. That we would end up no longer being able to cope with the system. Every error would trigger a real chain reaction in design, production or spare parts distribution. The whole thing was like open-heart surgery. Based on our good experience, we gave the experts at cubikom the benefit of the doubt: We trusted that they would be able to get everything under control in our interests."
Decision for the more flexible CAD PDM system. Implemented by experienced hands.
"We had Autodesk's recommended follow-up product, Autodesk Vault, demonstrated to us. Ultimately, however, we decided on GAIN Collaboration.
Firstly, GAIN Collaboration is very similar in terms of its structure and administration to the PSP we are familiar with. Secondly, it could be adapted for our special data transfer so that my colleagues and I can continue working without losing data and with the familiar links," says Jungbluth. "In addition, we were promised that the planned changeover would take place in the shortest possible time."
In fact, the transfer of the existing architecture was tricky: the existing logic had to be prepared in such a way that the old data could be mapped in the new system without any loss of information. The transfer took place in several steps, previews were generated in advance.
In the end, only a delta migration was necessary and the changeover could be carried out on a Saturday.
Smooth data transfer
"It certainly took a few days, but in the end all the data was transferred in the best quality. Before the transfer, all the data was automatically updated to the latest version level via GAIN Collaboration. Everything went smoothly," says Mr. Jungbluth with satisfaction.
Play it safe with cubikom
Jungbluth: "After the data transfer, we set up a few projects directly in GAIN Collaboration. Then a test run started: Our familiar system remained in place for a while - the new one was integrated in parallel. During this time, it quickly became apparent that everything was working as desired. And that all data could be accessed again as we were used to. During this time, the GAIN software system partner cubikom supported us intensively with training and support with further adjustments. So everything went quickly."
Quickly found in GAIN Collaboration
"GAIN Collaboration has met our expectations in terms of functionality, overview and level of comfort," says Jungbluth. "Of course, switching always means getting used to something. However, with GAIN Collaboration we all found our way around quickly and intuitively. For example, checking in and out using drag and drop is very convenient. Or the interface, which we can now adapt ourselves to how we want it."
The Baesweiler mechanical engineering company now also manages image and neutral data such as PDF documents under GAIN Collaboration. Everything can be stored as usual in a project-, function- and customer-related manner. Important additional programming in the product stream has also been made available again in Gain Collaboration.
You can rely on cubikom
Jungbluth is very satisfied with cubikom's commitment: "In addition to adopting our special data architecture, cubikom also made it possible for us to display customer numbers with commission numbers directly in the project list window. So we now have direct access again like before. cubikom has always reacted quickly, provided support and implemented things. You can rely on them. All promises have been kept."